Understanding Foam Moulding and Its Benefits
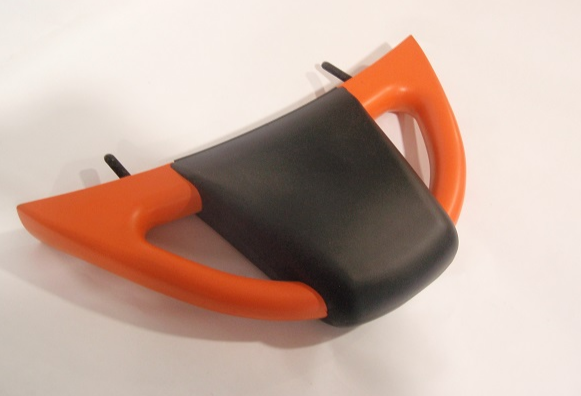
Foam moulding is a widely used manufacturing process that creates versatile and durable products from polyurethane foam. This process involves injecting liquid polyurethane into a mould, allowing it to expand and form a solid structure with a self-skinning surface. Polyurethane foam mouldings are known for their strength, flexibility, and lightweight nature, making them suitable for various industries, including automotive, marine, and furniture manufacturing.
One of the key advantages of polyurethane foam moulding is its ability to produce products with an integral skin. This self-skinning property provides a tough, tear-resistant outer layer while maintaining a soft and cushioned core. The moulding process can also incorporate textures, such as leather-like finishes, making it ideal for applications such as grab handles, armrests, headrests, and seating components.
The Polyurethane Foam Moulding Process
The polyurethane foam moulding process consists of several steps to ensure high-quality and durable products:
- Material Preparation – Two chemical components are mixed, triggering a reaction that creates foam expansion.
- Mould Injection – The liquid mixture is injected into pre-designed moulds.
- Curing and Trimming – After solidifying, the product is trimmed to remove excess material.
- Surface Treatment – Additional coatings, such as UV-resistant paints, can be applied to enhance durability and color stability.
- Final Inspection and Dispatch – The finished products undergo a quality check before delivery.
This method ensures precision in manufacturing and allows customization in terms of density, hardness, and appearance. Polyurethane foam moulding is essential in industries requiring both comfort and durability.
Applications of Polyurethane Foam Moulding
Polyurethane foam mouldings are used across multiple industries due to their flexibility and resilience. Some of the common applications include:
1. Automotive Industry
- Grab handles
- Gear stick knobs
- Armrests and headrests
- Steering wheels
2. Furniture Manufacturing
- Seating components
- Decorative trims
- Upholstered foam elements
3. Marine Industry
- Protective padding
- Boat seating
- Foam insulation
4. Safety and Industrial Products
- Shock-absorbent materials
- Protective gear components
- Machine padding
5. Gaming and Leisure
- Ergonomic gaming chairs
- Foam-based accessories
- Recreational equipment padding
Key Benefits of Polyurethane Foam Moulding
1. Durability and Strength
The self-skinning properties of polyurethane foam ensure a durable outer layer, protecting against wear and tear. This makes it ideal for high-use applications such as automotive interiors and office furniture.
2. Lightweight and Flexible
Despite its strength, polyurethane foam is lightweight, making it easier to transport and install in various applications.
3. Customizable Design
Manufacturers can create a variety of textures, densities, and colors, making it possible to match specific customer needs.
4. Resistance to Environmental Factors
Polyurethane foam mouldings are resistant to moisture, UV rays, and temperature fluctuations, making them suitable for both indoor and outdoor applications.
5. Comfort and Ergonomics
With its soft yet supportive nature, polyurethane foam is widely used in ergonomic furniture and seating solutions.
The Role of Acoustafoam in Polyurethane Foam Moulding
Acoustafoam, with over 36 years of experience, specializes in producing high-quality polyurethane foam mouldings. The company provides bespoke mould design and rapid prototyping, ensuring customer-specific solutions. Their integral skin PU foam technology offers high durability, flexibility, and customization.
Some of the unique offerings by Acoustafoam include:
- Integral Skin Foam Moulding – Providing a protective and textured finish.
- Elastomers (Rigid & Flexible Foam Moulding) – For shock absorption and structural support.
- Impact Foam Mouldings – Designed for applications requiring impact resistance.
- Insulation Foam – Used in thermal and acoustic insulation solutions.
Quality and Innovation in Polyurethane Foam Moulding
The key to producing high-quality polyurethane foam mouldings lies in precision tooling, material control, and strict quality checks. Acoustafoam follows a comprehensive approach to ensure:
- Accurate mould designs
- Proper material filling techniques
- Controlled curing and trimming processes
- Stringent final inspections before dispatch
With its advanced manufacturing techniques, Acoustafoam delivers polyurethane foam products that exceed industry standards, providing reliability and longevity.
Read also: Financial Foundations: How Smart Planning Leads to Business Stability
Conclusion
Polyurethane foam moulding is a crucial manufacturing process offering durability, flexibility, and customization across various industries. Its self-skinning properties make it an excellent choice for automotive interiors, furniture, marine applications, and industrial safety products. Acoustafoam stands out as a leader in this field, offering innovative and high-quality foam moulding solutions tailored to customer needs.
Whether for comfort, protection, or aesthetic purposes, polyurethane foam moulding remains an essential technology in modern manufacturing, contributing to the creation of durable and versatile products. As advancements in material science continue, the applications of polyurethane foam are expected to expand further, offering more innovative solutions for diverse industries.